As most manufacturers know, audits, inspections, follow-up services and reviews are all different names for the same function: ensuring that products that were originally tested and certified still maintain the same high standard years after they originally came on the market, or that modified products meet all the applicable requirements.
Audits are conducted by a third party agency or conducted internally by the manufacturer’s own quality control staff or an outside agency. They may include such things as a review of personnel, materials, finished product and quality control procedures. As a test laboratory, we undergo audits just as any manufacturer would. Audits may be conducted by our various accrediting agencies to ISO 17025 or internally by our own quality control manager and staff.
Lab personnel are audited to ensure they have the highest quality of training. Knowledge of test standards, test procedures, equipment and instrumentation are all part of the employee’s review.
Equipment and test instruments are audited to ensure they are in continuous calibration and being maintained in good working condition. Calibration must be traceable to NIST standards. Equipment and instruments are also monitored to ensure that if found defective, they are immediately removed from service and tagged so that they cannot be used by mistake. The work environment is audited to ensure that employees have safe and sanitary working conditions.
Project files are audited to ensure that proper documentation is included of the samples received for testing. This may include, but is not limited to, the actual number of samples received for testing, tests performed, the results of the tests and drawings, installation instructions and photographs and any other documentation required to accurately describe the product received. Laboratory procedures are monitored beginning with the purchase order, receipt of samples for testing to the issuance of the final test report and samples disposal. Procedures for receipt and storage of samples and project files are monitored to ensure that samples and files are kept safe and confidentiality will not be breached.
Other audited procedures include: maintenance of our library of current test standards, calibration procedures and certificates, procedures for training of lab personnel, complaints, and management. These are all part of the auditing process.
Supplies purchased for use in testing must be strictly monitored. Prior to a purchase order being issued for the acquisition of supplies, lab management must first check the purchase requisition against the appropriate test standard. Once the purchase order has been placed and supplies received, our quality control manager must verify they are correct before they can be used in testing. Records of all test media are maintained.
Even the issuance of a test report has a procedure that must be audited to ensure that the sample tested can be traced back to a test report and project file. Each report must be assigned a unique report number that references specific information as to the date samples were received, what tests were performed, test results and a statement whether or not the product complied with the test procedure.
The IAPMO R&T Lab staff has been trained to meet the guidelines of the ISO 17025 standard and our equipment and calibration meets or exceeds the requirements outlined in ISO 17025.
Our accreditations by IAPMO R&T, Inc., NVLAP, IAS, IAPMO R&T Oceana, CSA, ASSE, HUD, City of Los Angeles, Commonwealth of Massachusetts and many other organizations prove that we are leaders in the testing industry.
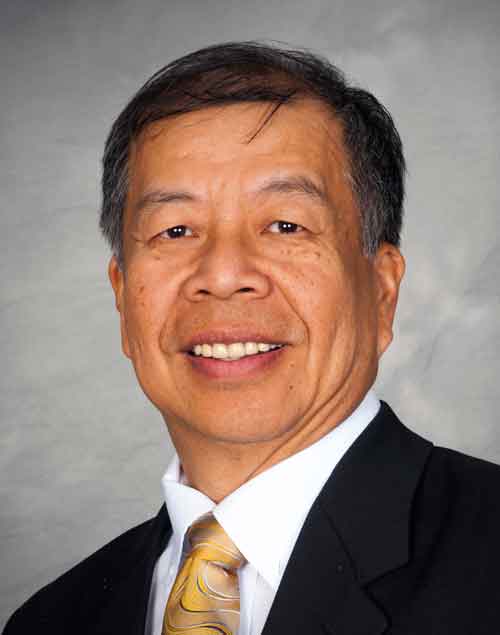
Ken Wijaya
Last modified: December 29, 2022