People reading this article are for the most part aware of the importance of backflow prevention and cross-connection control. We know that backflow prevention assemblies, methods, and devices are vital pieces in protecting the water systems that we use in our everyday lives. The installation of cross-connection control protection is mandated in all three model plumbing codes – the Uniform Plumbing Code® (UPC), the International Plumbing Code® (IPC), and the National Standard Plumbing Code® (NSPC).

These codes give us direction on the proper protection required to be installed in specific applications, such as lawn irrigation or fire protection systems. They also spell out what is required for fixture, equipment, or appliance protection. In addition, the codes also mandate testing requirements for backflow prevention assemblies and require the use of certified testers to carryout the required testing. We have rules and regulations in place to protect the public health, but still, problems exist.
As buildings are built, several inspections occur. In a typical project, the plumbing and mechanical systems are included in the plan review process. After that, at a minimum, there are several on-site inspections. These include the rough-in inspection, and then after the installations are complete, the fixtures are set, and other equipment is installed, a final inspection is conducted. During the plan review process, problems with the system design should be identified. However, that is not always the case. In the photo at the top of this page, you can see a large combined water service entering a building. This service is providing water to both the fire protection and the domestic water system. This installation as installed per the approved building plans developed by a licensed engineering firm. The plans were reviewed and approved by two separate jurisdictions. It was installed by a licensed contractor and inspected by a certified inspector working for a third-party inspection company. From start to finish, the installation is incorrect and all parties involved failed to recognize the problem. Who is to blame here? Is it the designer? The inspector? The contractor? The plan reviewer? Is it everyone? Or is it no one?
Looking at the photo, can you see the issue? There is no backflow prevention protection installed on the fire system. In the meter vault outside the building, there is a double check valve assembly installed in the vault on the combined service after the water meter. This will provide containment protection to the service, but if pressure is lost within the building, there is nothing protecting the domestic service from the fire service. This installation still exists as pictured, as do many installations that are incorrect. Even when the problem is pointed out, the question then becomes who is to blame and who should pay to make the installation correct? In most cases, no correction is made. That is why the inspections are so critical. It is also why we need better training at every level of the industry. Several individuals had the opportunity to correct this issue both before and after the installation took place, but it somehow fell through the cracks – or more accurately, the holes – in our systems.
What is the problem? It is a lack of education and training for each part of the process. There are also weaknesses and a lack of specificity in parts of the regulations. The IPC, for example, requires assemblies to be accessible without defining what that means. Is a backflow prevention assembly 40 feet in the air really accessible? See the photo below.

Without the proper definition of what is accessible, it is left to the designer, installer, or inspector to make that decision. A third-party inspector who has limited knowledge of backflow prevention assemblies may not realize that the valve must be field tested on an annual basis at a minimum. The UPC and NSPC state that any assembly mounted more than five feet above the finished floor must be installed with a permanent platform for testing and maintenance. In truth, even if a 40-foot height is allowed by code or regulation, common sense should be used when designing, installing, or inspecting plumbing installations. Any valve that requires service on a regular basis should be installed in a location that takes that into consideration. We need people who understand the entire system, not just a small piece of the puzzle.
Looking at other common problems, we see reduced pressure principle assemblies installed in pits, or vacuum breakers installed below the flood level rim of fixtures. Chemical dispensers have similar issues in many areas. Some items are installed after the final inspection by untrained people. Many things we find wrong have been installed by licensed individuals who should know better, and inspected and approved by inspectors who are unfamiliar with the code requirements on the equipment or fixtures they are inspecting.

Vacuum breakers on flushometers is the perfect example. We all need to do a better job of educating everyone in the industry. When I was working in the trade, I saw many tradespeople that knew how to install plumbing and mechanical systems. They could follow a shop drawing or a blueprint and install any system perfectly as drawn. They did not know, or in some cases even care, how the systems they installed worked. They considered themselves simply a piece in the puzzle. Inspectors and designers need to be more than that. While being a piece of the puzzle, they need to understand the complete puzzle. They need to know how each piece works within the puzzle.
People who are reading this article are looking for a better understanding of the puzzle. They are the individuals who want to understand the entire system – to know how to treat the problem, not just the symptom. They are the people who need to point out problems, who need to work with the inspectors, designers, and plumbers to make them understand the system, not just a small part of it. Malcolm X said, “Education is the passport to the future, for tomorrow belongs to those who prepare for it today.” Share your knowledge and the world will be a better place.
Article first published in Working Pressure magazine
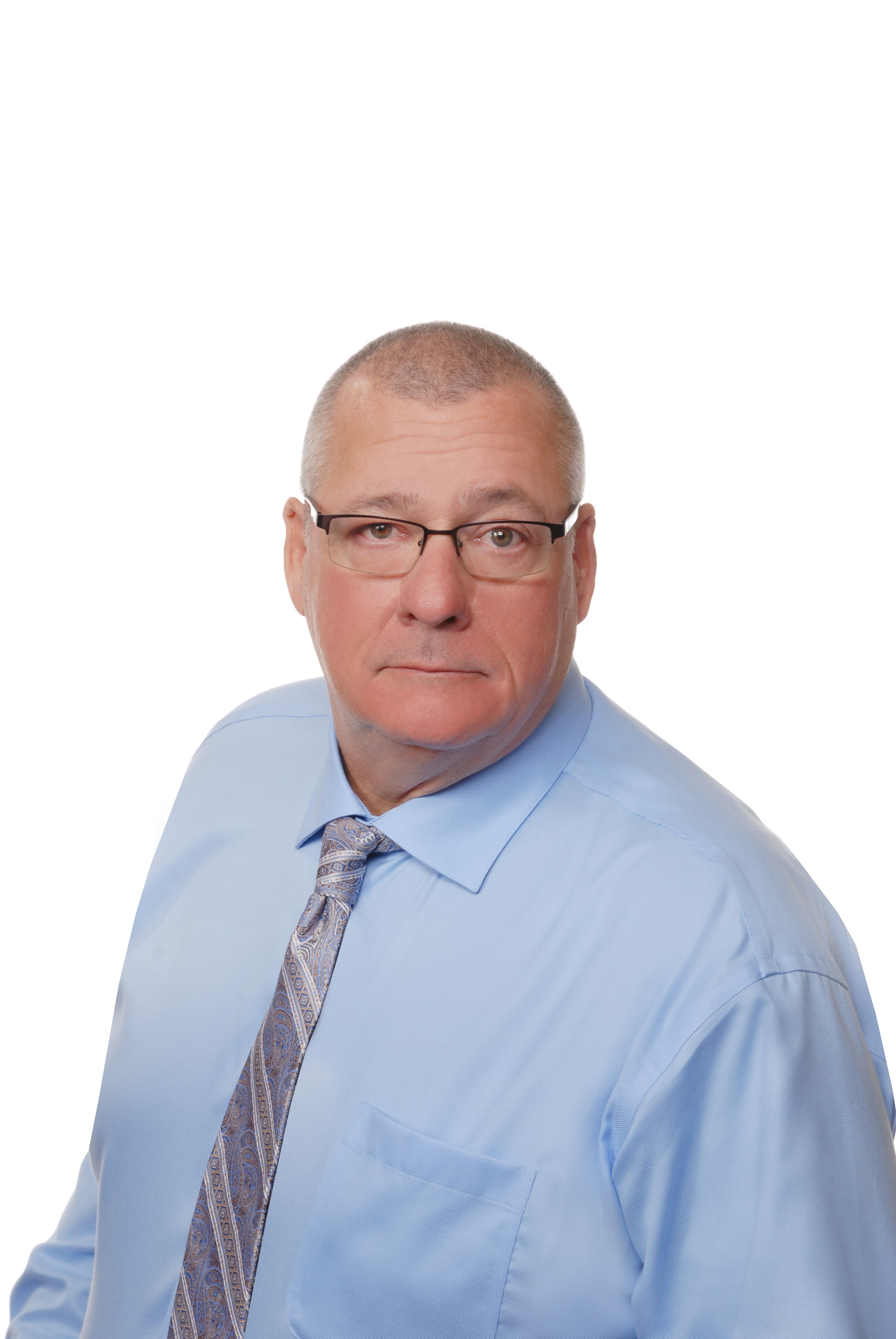
Sean Cleary
Sean Cleary has been a member of United Association Local 524 Scranton, Pa. for more than 40 years. He has worked in all phases of the plumbing and mechanical industry, and is a licensed master plumber. Cleary is a past president of ASSE International and past chairman of the ASSE Cross-Connection Control Technical Committee. He is employed by IAPMO as the vice president of operations for the Backflow Prevention Institute (BPI).
Last modified: December 19, 2023