The Drinking Water System Components – Health Effects standard is one of the most tested and certified criteria in plumbing products. It, like most standards continues to evolve as new challenges and new products are included in its scope. There are several substantive changes that have now been adopted that directly impact manufacturers with existing test reports and certification.
Among the changes are those requiring more rigorous conditions for testing. By increasing the objectivity of the testing, the result will provide more consistency. This raising of the bar is good for the manufacturers and consumer by keeping marginal products from reaching the market.
Copper pipe, tubing and fittings made from C12200 are now excepted for analysis for regulated metals release under pH 5 test condition providing the manufacturer include a statement to clarify that condition (see Section 4.5.3.2). C12200 (or DHP Copper) is commercially pure copper, that has been deoxidized with phosphorus, leaving a relatively high residual phosphorus content. C12200 is not susceptible to hydrogen embrittlement but has relatively low electrical conductivity due to the amount of phosphorous content. C12200 is frequently used in heat exchangers, kettles, distilleries, condensers, and medical gas lines.
Stainless steel inserts in PVC, CPVC and PP transition fittings are also normalized to the wetted area and internal volume of the fitting, not the wetted area and volume of the plumbing system. (see Section 4.7.2.2). As more manufacturers start to use stainless steel in fittings it is proper to give this material the same level of exception as copper. PEX systems with stainless steel inserts are still normalized to the surface area and volume of the system they are installed in.
Added guidance on subtraction of naturally occurring beta particle emitters, like potassium 40, and threshold for gross beta speciation has been added and added methods for nitrosamine analysis (see Section N‐1.7.4.5) were better defined. This does not extend the time that the reagent water at different pH 5, 6.5, 8 and 10 is held inside the tested products only adds additional organic compounds that that the broad-based scanners (one for organic and one for heavy metals such as lead) will identify. The duration of the test varies however products like faucets are tested for 19 days.
Which method to use to monitor specific nitrosamine compounds has been clarified in N-1.6.4.5.
Additional quality control requirements have been added to the monitor the exposure waters specified in the Standard. These additional controls will help ensure that different laboratories obtain similar results.
As a result of testing water in childcare facilities, the State of California Division of drinking water recommended that faucets used comply to Statistic Q of 1 or less for lead. The Drinking Water Additive Committee of NSF International has revised the NSF/ANSI/CAN 61 Standard, to require a complying faucet have a Statistic Q value of 1 or less. This requirement is scheduled to be published in the 2020 version of the Standard. The goal of the Standard is product certified under the old requirements should be brought to compliance by 2024.
CA AB 2060 is a new regulation that is still being debated. If accepted as currently proposed, the bill will model the same Q values as the soon to be published NSF/ANSI/CAN 61 but the implementation will be staggered over the next three years for manufacturers, (20% of products compliant by July 1, 2021; 40% by January 1, 2022; 75% by January, 1 2023, and 100% by January 1, 2024.). The Bill was approved by a 5-0 vote of Senate Environmental Quality Committee on August 11 and will be reviewed by the Senate Appropriations Committee during the hearing on August 17, 2020.
Manufacturers not keeping their products certified to the Safe Drinking Water Act endangers the entire chain of distribution. Everyone from the engineer who specifies and accepts the product to the wholesaler to the contractor who installs the fixtures and fittings to the building owner, everyone can be made to share in the cost of removing and replacing noncompliant products. These are necessary steps, not just red tape or a tax to bring complaint products into the marketplace for everyone’s health and safety.
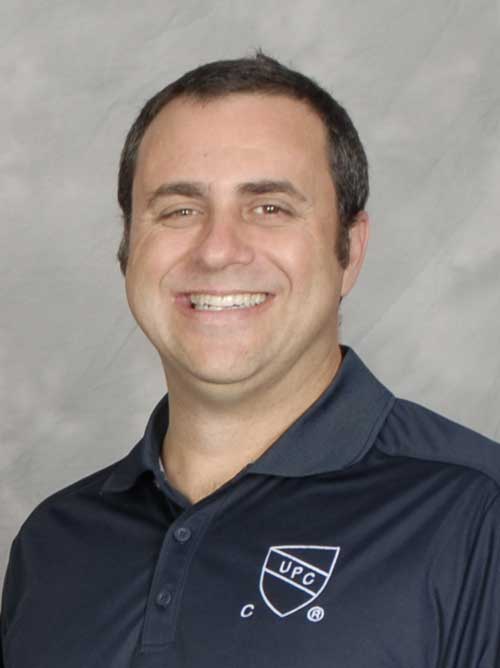
Kyle Thompson
Last modified: July 14, 2023