Easier Said Than Done
September 2006, California passed lead free plumbing legislation, AB1953, which was later incorporated into the California State Health and Safety Code under section 116875. California’s Health and Safety Code stipulated that as of January 1, 2010, “any pipe or plumbing fitting, or fixture intended to convey or dispense water for human consumption” introduced into commerce within California would be limited to a “weighted average lead content of the wetted surface of not more than 0.25 percent. Solder or flux was limited to 0.2 percent.
California added legislation in 2008, directing the Department of Toxic Substances Control (DTSC) to enforce the law and requiring manufacturers to have their products certified by an independent ANSI-accredited third party. Other states such as Vermont, Maryland and Louisiana soon followed with similar laws. Lead in plumbing products was becoming a national issue.
The federal government took notice, and a bill was introduced into the U.S. House of Representatives and Senate about reducing the amount of lead in plumbing products, solder and flux. The bill soon passed and was signed into law. Beginning January 4, 2014, federal Public Law 111-380, the Reduction of Lead in Drinking Water Act, amends the Safe Drinking Water Act to include a formula for measuring the weighted average lead content of a pipe, pipe fitting, plumbing fitting or fixture. In addition to the 0.25 percent lead limit on wetted surface areas of fixtures, the law sets the benchmark for solder and flux at 0.2 percent.
The EPA has indicated that it will enforce the new requirements, and is preparing guidelines for testing, certification and enforcement. The federal law contains no guidelines or methods for testing and certification. Many manufacturers have already started using lead free alloys in their products to meet the deadline.
Uncertainty in certification
“There have been a lot [of] questions over the past few years about Public Law 111 -380,” said Jin Luo, senior director of IAPMO R&T. “The EPA, working in conjunction with manufacturers, certification bodies and other interested parties, is trying to develop a set of guidelines and procedures to make sure that consumers are protected and manufacturers are clear on their duties and obligations in meeting the law. Public Law 111 -380 is very specific on the calculation to determine compliance. The information goes into a table, is summed, and produces a number that’s the weighted average of lead in the components of a product. The test method has not been finalized for the federal lead law. California had a similar issue when AB 1953 was enacted, and consequently developed a testing protocol several months after the Jaw went into effect.”
The EPA is investigating the use of NSF 372 as a testing protocol, but has not yet finalized its decision. In response to a question about whether certifying products to NSF 372, and not Public Law 111-380, could create problems for manufacturers, Luo pointed out, “NSF 372 has not been formally adopted by the EPA.”
Manufacturers also referred to the California DTSC testing protocol and to NSF 372 in response to the question of whether products that were coated or acid washed to remove lead could qualify for certification. According to Jeremy Brown, codes and regulatory manager at NSF International, “Essentially, a coating doesn’t count because you can’t rely on its longevity. As far as de-leading technologies or washes, the actual analysis should be performed on the product prior to the use of those removing technologies. Both the DTSC testing protocol and NSF 372 require the coating be removed and the base alloy tested.”
Ultimately, the EPA has the power to interpret these laws and should be consulted for guidelines as to whether or not a product falls within the scope of the law. As for the argument that “human consumption” had to be a product’s primary function, the law doesn’t address what primary is, and in the absence of that, “human consumption” is going to be defined very broadly.
Regardless, cautious manufacturers needed to ask themselves, “How do I minimize my exposure to lawsuits?” And with no best practices yet on how to do that, in many instances, the answer to that question was they would need to consult an attorney.
Time is the bottom line
Ratcheting up the pressure on manufacturers and distributors eager to get products to market, many customers – especially municipalities – were requesting lead free products and had been for some time.
Michael Tharpe, chief inspector of the Los Angeles Plumbing, Mechanical and Fire Sprinkler Division, said the federal Reduction of Lead in Drinking Water Act is similar to California AB 1953 by “placing the burden on the
manufacturers for verification of compliance with the new law.” One way of achieving this is through third-party certification by an ANSI-accredited certification body.
Jurisdictions are going to be looking at third-party certification, as they don’t want to be responsible for verification. When the certification body completes its review of the testing and evaluation, the body lists a certificate on its website showing compliance to the federal lead law, and the manufacturer receives the acknowledgement that the product is certified. This is what many jurisdictions will require to show compliance to the federal statute.
As to the amount of time required for certification, certification bodies depend on a number of factors in the speed to market. “If the product being tested is a faucet that has absolutely no certification, it may take longer to test than, say, a simple product like a flexible connector,” Luo said. “A fitting made of homogenous material can be done in a matter of a few weeks. It all depends on the product and the difficulty of obtaining formulation information.”
Despite the things learned when California, Vermont, Maryland and Louisiana enacted similar legislation, there will be questions and further clarification after the 2014 federal deadline. Historically, there have been “transitional periods,” during which legislation or other means would be required for clarification. Until then, strict compliance with the law is advised for all manufacturers.
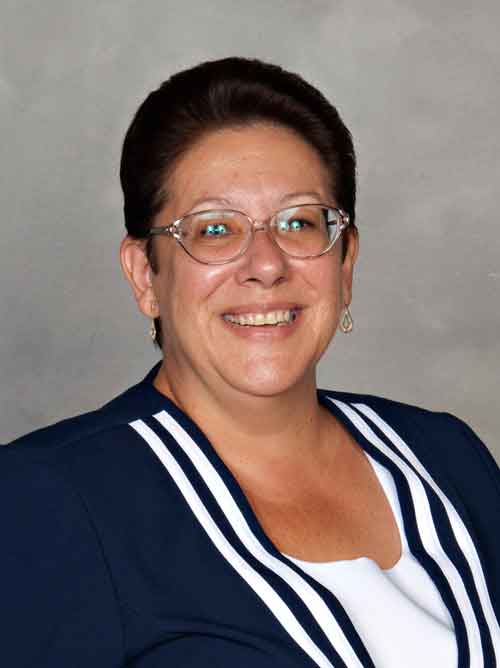
Donna Estrada
Estrada has worked for laboratories for nearly 40 years, helping manufacturers in testing and certifying their products in the United States, Canada and Mexico.
Last modified: July 14, 2023