Is the testing of backflow prevention assemblies on fire systems different than testing the backflow prevention assemblies on domestic water systems? The correct answer to this question is both yes, it is, and no, it is not. There are additional steps to take in preparation to the testing and after the completion of any backflow testing on assemblies installed on fire protection systems. The fact that you are a certified tester does not mean you are qualified to work on a fire protection system. Many jurisdictions have specific rules and regulations regarding any individual or company that is working on any component of a fire protection system, including the backflow protection on these systems.
Before any certified tester considers performing a field test on the backflow assembly of a fire protection system, they need to, at a minimum, have an understanding of the system itself. There are several different types of systems that have specific needs or challenges related to the process of shutting valves and also to reopening them after a field test is performed. In most cases, an alarm system is also in place, which must be placed on test to prevent a fire company response in some cases. The first part of any field test is identifying the backflow assembly type and then matching it to the level or degree of hazard of the fire system. To do that a tester must have a basic understanding of the fire system itself.
The degree of hazard of the system will either be high (health) or low (non-health) and the backflow prevention installed must provide the correct level of protection to meet the degree of hazard. In low hazard situations, with the exception of some residential fire protection systems, the backflow protection at a minimum must be a double check valve assembly (DCVA) or a double check detector assembly (DCDA).

There are several factors that must be considered when assigning a degree of hazard. These include fire department connections, fire pumps, chemical additives, system type, and other factors. If the system is a high hazard situation, then the minimum protection would be a reduced pressure principle assembly (RP) or a reduced pressure detector assembly (RPDA). Once a tester confirms the correct degree of hazard, they should look at the assembly itself.

Shutoff valves on fire protection systems must be indicating valves according to the National Fire Protection Association (NFPA). That means there must be a visual indication of the valve’s current status (open or closed). If it is a gate valve, it must be an outside stem and yoke valve (OS&Y valve). The use of non-rising stem gate valves on fire systems is prohibited. Butterfly or ball valves on backflow assemblies will have indicating paddles to show their positions.

In addition to being indicating, the shutoff valves must also be supervised. This means the shutoff valves must be locked in position to be electronically monitored. Testers must understand the importance of ensuring shutoff valves are properly closed and then reopened after the backflow field test is complete. One of the leading causes of the failure of water-based fire protection systems is broken or closed valves in systems. If you fail to open a shutoff valve when testing a backflow assembly on a domestic water system, it may cause an inconvenience. If the same thing happens of a fire protection system, property damage or injury may occur.
Another consideration related to shutoff valves on backflow prevention assemblies is what do you do when testing the assembly installed on a fire protection system? The assembly must be placed in a static condition for the testing. To do that using any recognized field test procedure, you must at a minimum close the number two shutoff valve. In some recognized field test procedures, you will need to shut off both the number one and number two shutoffs. After completing the field testing of the backflow assembly and returning the shutoff or shutoffs to the fully open position, you are required by NFPA 25 to conduct a flow test to ensure they have opened. This requires at a minimum a main drain test and may require a forward flow test. If a certified backflow tester does not know how to do this testing, they must have an individual who does have that knowledge complete the flow testing to consider the fire protection system returned to service. Some testers believe since the fire system is already in a static condition the shutoff valves do not need to be closed, however, to follow the field test procedure the shutoff valve must be closed. That is not correct. Also leaving the number two shutoff open and then attempting to test the second check with backpressure may cause any number of issues, from tripping flow switches to dry valves and may also lead to incorrect readings and inaccurate test results. Some testers also believe flow testing after returning the system to service is not needed. The liability they bring on their company by not following the correct requirements is significant.
Looking at the fire protection system, other considerations are related to system type. In a normal wet pipe fire protection system containing only water, a DCVA or DCDA is the code required protection. When a tester looks at this system there are several things for which to look. Does the system include a fire pump? We need to ensure the fire pump is not activated as a result of our testing. Does the system contain a fire department connection?

Fire department connections normally do not affect the degree of hazard unless there is an alternate water source within 1,700 feet of the connection; if there is, the double check protection is incorrect and the system is a high hazard. The issue is the fire department may draft water from that alternate source in fighting a fire. It could be a river, lake, the ocean, or another source of unknown quality. Another issue is antifreeze loops on wet based systems. These may be used in limited areas where there in unconditioned space and may only be a small percentage of the entire system, but their existence changes the hazard level to high hazard. Chemicals may have also been added to the system to prevent microbiological growth and future system leakage. These chemicals also require a high hazard rating on the entire system.

Other water-based protection systems include standpipe systems, dry systems, pre-action systems, and deluge systems. Wet based standpipe systems are low hazard and require low hazard protection. Dry systems used in unconditioned areas use a dry valve that simply put has a check valve, which holds the water side and the dry side separate. The dry side is pressurized with air. When a sprinkler head opens on the dry side the air pressure drops, allowing the water side to push the dry valve open and flood the system. Certified testers conducting field testing on these systems need to understand the act of closing the number two shutoff valve on the backflow assembly may raise the pressure downstream of the shutoff valve enough to increase the water pressure and trip the dry valve, flooding the dry system. If the dry system is feeding an area like a sub-zero freezer, the results of that mistake can be very expensive. Tripping the dry valve will also activate the alarm system and bring the fire department unless the system was placed in test mode. Preaction and deluge systems are activated when a fire event occurs either manually or with sensors. Care must be taken when testing on these systems. A basic understanding of the systems is needed by anyone, including certified backflow testers, when conducting any type of work on the systems.
Performing the actual field test procedure steps on an RP or DVCA will be similar for fire protection valves and domestic water systems. The field test procedures for RPDA or DCDA are different. These detector assemblies are only used on fire protection systems. The purpose of the detector bypass is to detect either leakage or unauthorized (theft) water usage on the system. Many water utilities do not meter fire protection services as a result of the cost and size of larger water meters. They instead use detector assemblies to monitor low flows. With the exception of flow testing, a fire protection system should not have water flow or usage unless it is activated. As a result, the industry developed the ASSE 1047 RPDA and ASSE 1048 DCDA. Using a small bypass around the main assembly these valves force the first two gallons a minute to flow through the bypass piping and flow indicator (water meter) while the main assembly remains in a static condition.
A traditional detector assembly bypass contains a small assembly of the same type as the main valve. When testing this type of detector assembly the tester performs a field test on the large assembly, and then a field test on the bypass assembly. Each assembly is isolated from the other assembly during the testing. The tester also ensures flow though the flow indicator (water meter) while testing the bypass assembly.
A type two detector assembly contains a single testable check assembly in the bypass. We all know that a single check is never considered backflow protection. With the type two detector assembly, the bypass begins after the first check of the main assembly to the bypass does have double check protection. With the type two reduced pressure detector assembly the bypass begins after the number one check on the main valve and in the reduced pressure zone, so it does have the same level of high hazard protection. When testing this type two detector assembly, the tester performs a field test on the large assembly, and then a field test on the bypass assembly. Each assembly is isolated from the other assembly during the testing. The tester also ensures flow though the flow indicator (water meter) while testing the bypass assembly.
As it was stated before, following any backflow field testing on a fire protection system assembly a flow test is required to ensure the fire protection system is operational. Remember to take the alarm system off test and return it to service. Make certain you have the credentials and insurance needed to test or work on these systems. Understand that the system must be placed back in service when you are finished; if the field test caused issues with the assembly it may need to be repaired in order to place it back in service. As I said at the beginning, testing on fire systems backflow assemblies is both the same and different.
Article first published in Working Pressure magazine
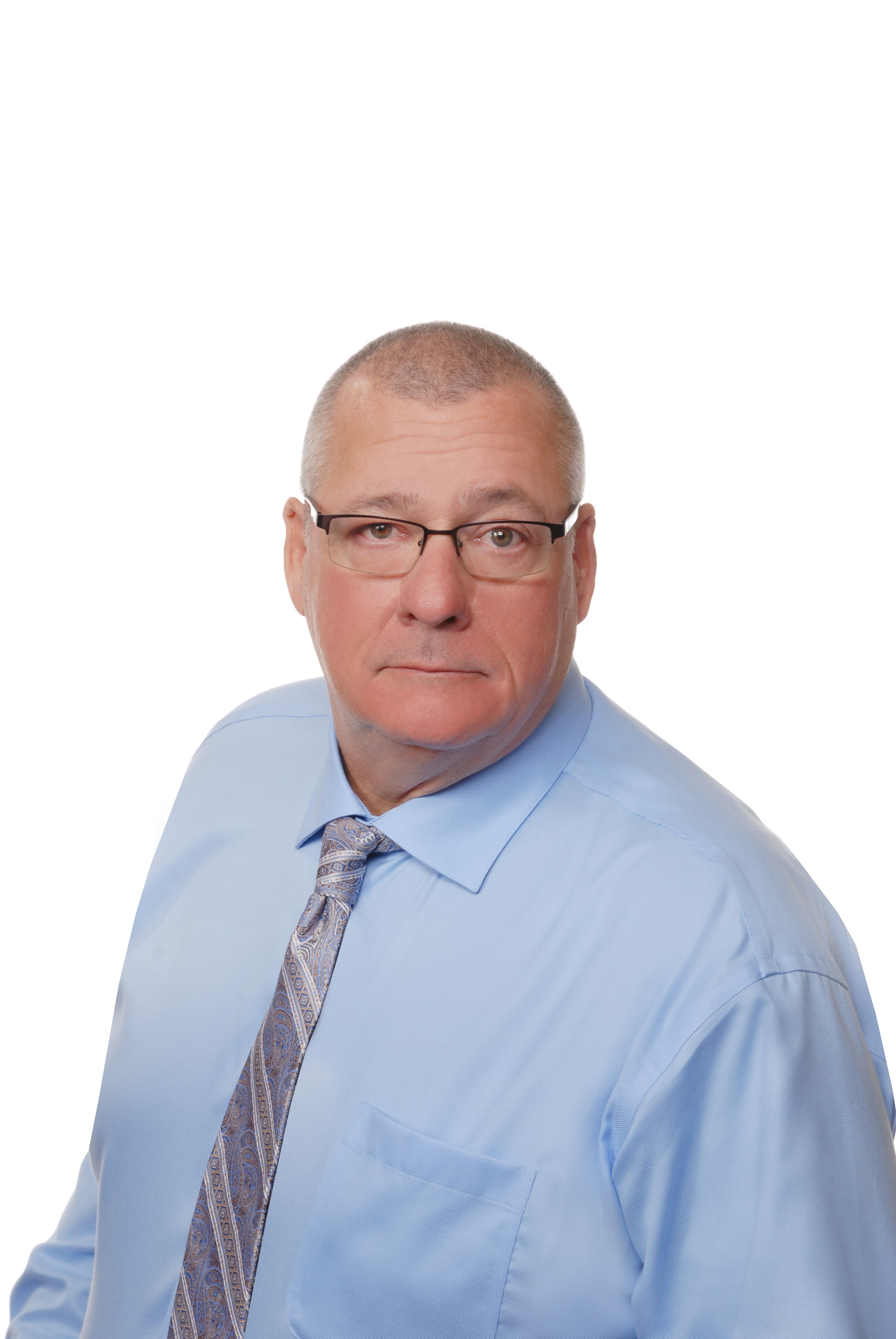
Sean Cleary
Sean Cleary has been a member of United Association Local 524 Scranton, Pa. for more than 40 years. He has worked in all phases of the plumbing and mechanical industry, and is a licensed master plumber. Cleary is a past president of ASSE International and past chairman of the ASSE Cross-Connection Control Technical Committee. He is employed by IAPMO as the vice president of operations for the Backflow Prevention Institute (BPI).
Last modified: May 8, 2024