Testing and certification is traditionally thought of as marking the conclusion of a product’s development, but it actually touches every aspect of the process. A manufacturer hoping to market its products within a specific jurisdiction cannot just design and build a product and simply hope when all is said and done that it meets all the applicable standards; more than a little forethought is required.
Typically the process works something like this: a manufacturer or inventor recognizes the need for a product or has conducted a survey that indicates the opportunity to fill a void with a specific product. Next they might perform a market study to determine whether or not it is possible to create such a product and/or that the product would be profitable.
Next, a budget is determined. How much will it cost to produce something like this product? Will it require a subcontractor to build it? Meanwhile, drawings are created from which a prototype will be designed and built.
During this important stage, the manufacturer/inventor wants to determine unequivocally whether or not the product will work properly and if the assembly makes sense. If the prototype checks out, a special version of the product is produced for testing and certification. After testing and certification, the manufacturer can begin marketing and mass production.
This is a simplified flow chart, obviously, but you get the idea. I also intentionally left one extremely important step out of the process — an oversight that has plagued many a product’s launch, sometimes sending it all the way back to the drawing board. I’m talking about the product’s adherence to health and safety standards.
Bottom line — you could have the greatest idea ever, a product that revolutionizes life as we know it. But if it doesn’t meet every requirement prescribed by the codes and standards that govern its use in a particular city, county, state or country, you can’t sell it there.
Wouldn’t you like to know the product is certifiably safe and healthy before you’ve invested tens of thousands of dollars and weeks to months of time designing and manufacturing it?
IAPMO R&T Lab is more than one of North America’s premier product testing facilities — we also provide dozens of related services, including consultation during the design and prototype stages of product development.
For manufacturers of plumbing and mechanical products, having IAPMO R&T Lab’s intimate knowledge of every regulation pertaining to a particular product’s use anywhere in North America could prove absolutely invaluable. The alternative could mean a very costly exercise in starts, stops and second and third attempts.
As a manufacturer, you don’t need to have a person on staff that knows everything — you just need to know where to find the necessary information. And you’ll find it with IAPMO R&T Lab.
Working with IAPMO R&T Lab as a consultant during the developmental stage of your product’s manufacture adds a little bit to the up-front cost, but the long-term savings — in time and money — could be immeasurable.
Take, for instance, a manufacturer that recently sent their newly invented toilet to IAPMO R&T Lab for testing in hopes of having it certified for North American use. The dimensions did not conform to United States standards, so the product failed in testing. The whole product had to be changed, meaning the manufacturer had to start all over again.
Had the manufacturer come to IAPMO R&T Lab first, before they even built their prototype, we could have pointed out quickly where the toilet as designed would violate the standards and suggest revisions they could make in order to be in conformity.
For more information on IAPMO R&T Lab’s consultant services, direct your Web browser to www.iapmortlab.org.
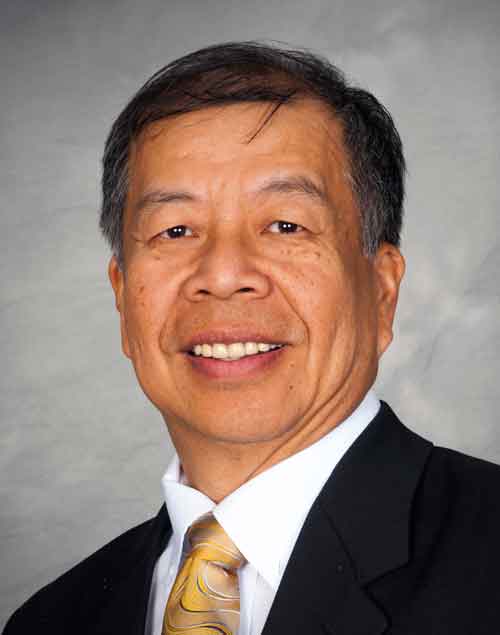
Ken Wijaya
Last modified: May 31, 2023