The installation of backflow prevention protection is an important part of internally maintaining the water quality within a facility through the use of isolation cross-connection protection. The installation of cross-connection protection at the service connection as containment protection protects the quality of the public water supply. Backflow prevention does not improve the quality of the water system – it works to maintain and protect the water that has been delivered to the facility from the public system or, in the case of isolation protection, maintain the quality of water supplied to the fixtures or appliances.
The quality of the water provided to the facility is a factor to be examined in a cross-connection control program. Little things like dirt and debris can have a significant effect on the reliability of backflow prevention assemblies and devices. The leading cause of check valve failure in backflow assemblies is dirt and debris getting into the assemblies. The quality of the water is something that the backflow installer or tester has little control over. We can install strainers upstream of the backflow protection to try to decrease the size or number of particles that reach the assembly, but that is never a 100 percent solution. In some system types, fire protection systems as an example, the use of a strainer may restrict the volume of water needed for the system if a large demand occurs. Even in domestic water systems, strainers that are not regularly serviced may cause pressure or volume issues. In a domestic water system, installing a regularly serviced strainer upstream of the assembly or device is a good proactive step to help with preserving the quality of water flowing downstream into the required protection. Any dirt or material we can prevent from entering the backflow preventer will help us in maintaining the assembly, both short and long term, in working order.
Other water quality issues that can affect backflow preventers include minerals in the water itself or chemicals added to the water as a disinfectant. Minerals can build up on internal parts and surfaces within the backflow device or assembly. This build up can restrict movement of the assembly parts and have an adverse effect on the rubber parts within the valve. (Photo 1) These minerals are a water quality problem that, depending on the severity of the problem, may require the installation of water softening or filtration equipment. The addition of chemicals to a system can also have an adverse effect on backflow assemblies and devices. An increase in chlorine levels can cause issues with internal parts. (Photo 2)



Over the past several years, as a result of a better understanding and concern about Legionella and other similar problems, system changes have been made. Some water suppliers or facility managers have added chemical feeders to their water systems in hopes of treating the water and removing biofilm from the piping interior in an effort to prevent issues with Legionella bacteria. When using this type of treatment, the problem is that a regular use of these feeders injecting chemicals into the piping system must occur. This, in some cases, can lead to human health risks and damage to water pipes, which corrode as a result of the long-term hyperchlorination. We need to understand that changing the chemical content of the water will also affect piping materials, along with fixtures, valves, and other fittings throughout the system. What solves one issue may cause, at times, more severe problems.
Aggressive water treatment is part of what created the lead water service issues in Flint, Mich. In some cases, the water services were in place for more than 70 years. It was the water treatment that broke down the protective film in the piping and started to release lead into the water. This same issue occurred in piping, valves, and equipment throughout the water distribution system, and in consumers residences and facilities. Changing one piece of a system can have a dramatic affect elsewhere in the system.
That is why when looking at cross-connection protection, we have to understand that we are only looking at one piece of a complicated and important puzzle. When we install backflow preventers, we change the hydraulics of a system. There is a cause and effect. It could be thermal expansion issues, a reduction in available pressure, the creation of a closed water system; the list goes on. Once installed, that protection needs to be tested and maintained. Water quality needs to be something we look at in any cross-connection program. If we find problems or failures in backflow prevention assemblies and devices, replacing them or repairing them is important. Equally important is answering the question as to why the failure occurred. Repairing or replacing the failed part is only one step in solving the problem and finding a long-term solution. A quality tester asks why the valve failed, then looks to discover the cause, and then, hopefully, makes the needed system correction. Water quality is a factor that must be considered in each and every valve failure.
It is the water company’s job to provide clean, safe drinking water. It is our job to maintain and, in some cases, improve the quality through the use of filtration or other treatments. We then need to create that one-way path to make sure backflow does not occur and cross-connections are eliminated or protected. Every person in this nation and in the world deserves access to clean, safe drinking water and it’s our job to do all we can to provide it.
Article first published in Working Pressure magazine
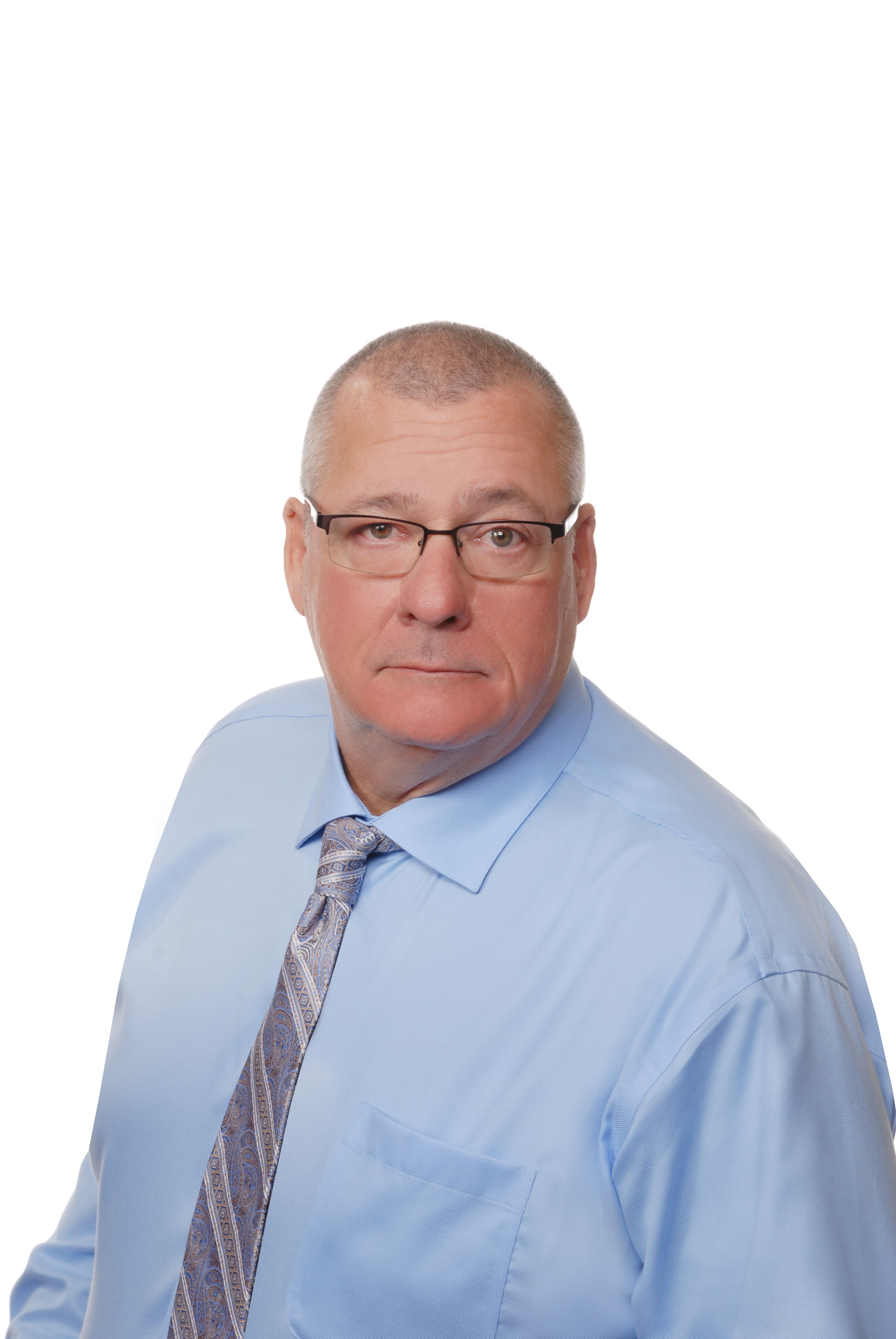
Sean Cleary
Sean Cleary has been a member of United Association Local 524 Scranton, Pa. for more than 40 years. He has worked in all phases of the plumbing and mechanical industry, and is a licensed master plumber. Cleary is a past president of ASSE International and past chairman of the ASSE Cross-Connection Control Technical Committee. He is employed by IAPMO as the vice president of operations for the Backflow Prevention Institute (BPI).
Last modified: December 19, 2023