One of the biggest driving forces to certification is regulatory requirements. If a government regulation exists that prohibits the legal sale of a product into a jurisdiction without certification, there is a very high probability that companies will obtain that certification. Recently, a ruling was passed down by the United States Environmental Protection Agency (US EPA) that requires certification for specific products to NSF/ANSI/CAN 372. This standard provides criteria ensuring that products evaluated to it do not contain a total weighted average of lead content higher than 0.25%. Certain states also have their own rules mandating such certification. Additionally, for residential drinking water treatment products that make health claims such as the ability to reduce PFAS, companies must first register those products in the state of California to legally sell in that state. This is connected because the premise for registration with the state is certification with a nationally accredited third-party certification agency. While it is not a prerequisite for the state of Wisconsin to have certification, all plumbed in products that are making any contaminant reduction claim must register with the state to be sold legally. However, if the product has obtained third party certification to the standards the state has recognized, additional registration with Wisconsin is no longer required.
Another significant driver for choosing certification lies with marketing needs. There are myriad reasons why your marketing team may want to see a certification mark on the product you are trying to sell. To start, the competition has certification. While it is certainly not true of all purchasers, if two products are next to one another and are equivalent in all aspects except one is certified and one is not, often the buyer will choose the certified product. Another scenario is where your new product is state of the art, capable of doing something to which the market has not yet been exposed. Trying to convince savvy buyers of a new technology or a laundry list of things a product can do is not an easy task to tackle. However, when you seek out the help of a third party to demonstrate the claims you make on the product are true, the convincing becomes less about trust in what the product can do and more simply about why the product is beneficial for your prospective client. And finally, while it is a sad truth, the reality is that some products out there are touting unwarranted claims. Certification is a great way to ensure your products do not get lumped in with a group of shady products.
Finally, certification offers you assurance that your own procedures are working and doing the job they need to do. Manufacturing is not a simple task. To the naked eye, or uneducated individual, it seems very simple; take one part and connect it to another part and so on. Most consider manufacturing a rote responsibility. However, the true tale about manufacturing is that the simplest of missteps on any given line can turn a product’s final production upside down. When a company has certified products, of the multiple steps required to maintain certification there are two worthy of calling out and detailing.
ONE: MANUFACTURING FACILITY INSPECTIONS
All certification agencies have a routine for conducting inspections of any location that manufactures certified products. A good portion of time during this audit is spent ensuring the facility has a robust quality control system in place. The types of things looked for in these audits include isolation of non-conforming product, verification of certification marks only being used on certified products, and confirming the product build is the same today as when the product was tested. Each time a product is certified, the company is required to fully disclose every part or material that is used in the construction of the end product. When an auditor goes to a facility, the lists that were provided are brought along and supporting documentation is checked and verified to ensure nothing has changed. The products going out the door are manufactured the same as the products that were evaluated in the beginning.
TWO: ROUTINE MAINTENANCE TESTING
There are multiple steps in the process to obtain certification. One of the most important is subjecting the product to a series of rigorous tests that challenge products beyond their normal use applications, such as materials safety (which verifies the products are manufactured with materials that will not cause harm through mere contact with water), structural integrity (which means that products under pressure will not lose their structure and cause flooding in a home) and performance testing (which verifies a claim of specific contaminant reduction is factual). Testing up front is imperative, as it is the founding principle of certification. However, when a product is certified, accredited certification bodies are obligated to perform regular re-evaluation of the products, which includes re-testing. While on the surface re-testing may seem duplicative if nothing has changed in the production of the product, there are benefits not always realized. I have discussed above that the manufacturing process is not as easy as it seems; a simple unintentional misstep in the manufacturing process can cause unintended consequences. An example includes a situation in which a line worker decided to start using a different hand lotion while on the job. This employee followed all the standard operating procedures in place and the products came off the line as they were intended to. It was discovered while performing materials testing, that the hand lotion was emitting harmful substances into the water. Had testing not been conducted on this product, the manufacturer would never have discovered that products were going out the door that had the potential to cause harm.
There are several accredited certifiers available from which to choose. It is important to do your homework and choose the one that is right for you and your certification needs.
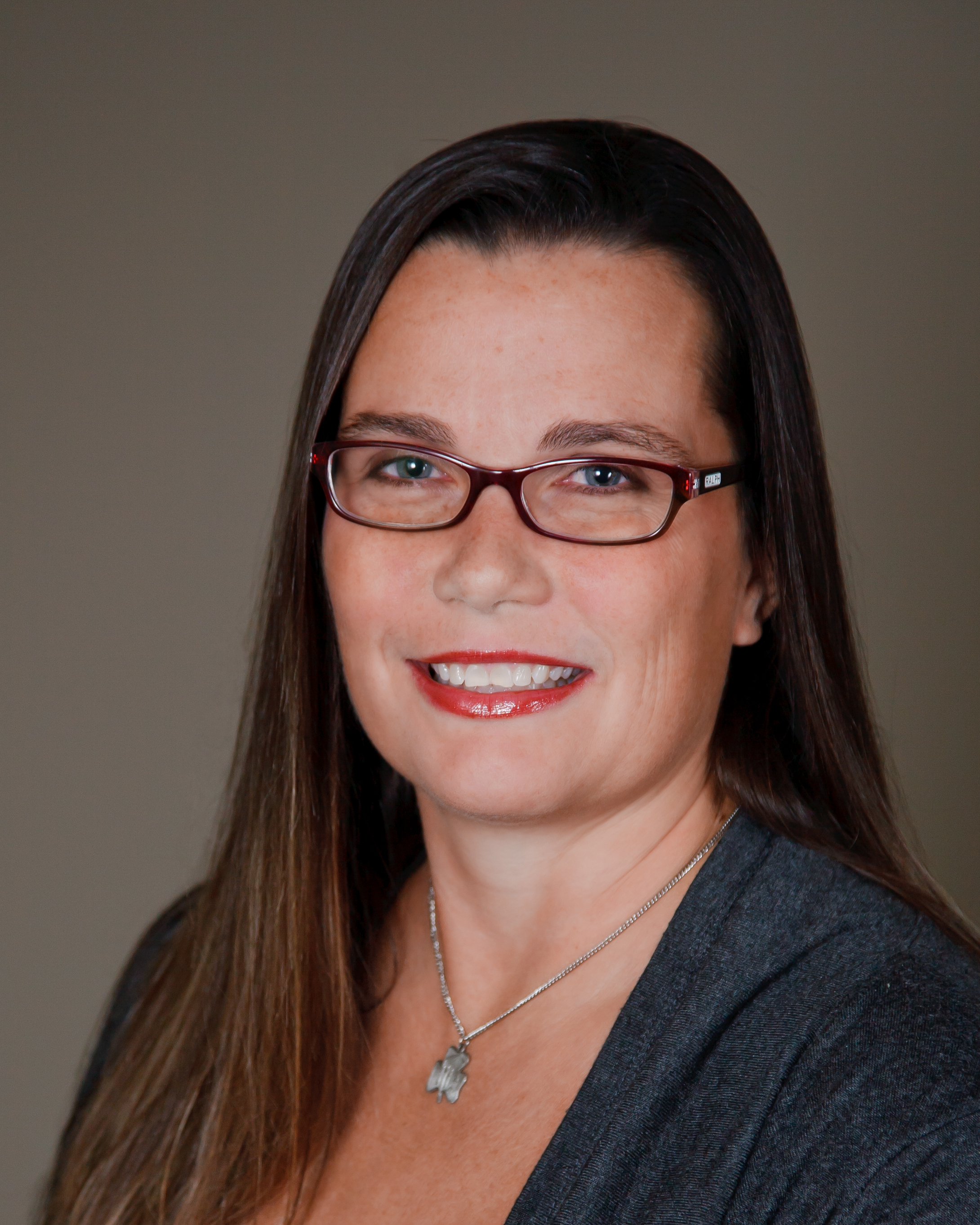
Tina Donda
Last modified: March 20, 2024