How new age digital water temperature controls have improved user outcomes and changed the way we evaluate institutional hot water system performance and the solutions we apply
Innovative technology and advanced new product development in water temperature control have delivered hardware and software that enable those responsible for hot water system design, operation, and maintenance to comply with key performance and measurement components of a Standard of Care.
A Standard of Care is defined as acknowledged applicable laws, standards, and guidelines. OSHA 1998, Joint Commission Environment of Care, ASHRAE Guideline 12-2020, ASHRAE Standard 188-2018, and VA Directive 1061 (2014) are relevant examples of Standards of Care that include critical recommendations for establishing and monitoring hot water system temperature control limits. Following a Standard of Care provides safe and comfortable user outcomes that minimize the risk of scald injury and protect against disease caused by waterborne pathogens such as Legionella.
TMV or DMV?
Armstrong International pioneered the first Digital Mixing Valve (DMV) over a decade ago with its Digital Recirculation Valve (DRV) called The Brain. This created an entirely new class of water temperature controls with highly specific application and performance characteristics. Prior to the DRV, mechanical room-based “Master Mixing Valves” were primarily thermostatic and originally designed for three-way “dead leg” water temperature control. As such, their application in a pumped recirculating hot water system is an adaptation that is inconsistent with the base product functional design.
A Thermostatic Mixing Valve (TMV) is designed to mix hot water at one temperature with cold water at a much lower temperature to deliver a mixed water temperature somewhere in between. TMVs were not designed to mix hot water with hot water, yet, in a recirculating hot water system operating at low or zero demand, that is exactly what they are asked to do! In fact, to get TMVs to function properly, some manufacturers suggest supplementary add-on devices, such as a manual throttling valve to control the amount of hot water that can return to the water heater or adding aquastats to turn pumps off to allow a system that is experiencing temperatures above a TMV’s set point, often described as zero demand “temperature creep,” to cool.

A New DMV ASSE Standard
The most influential standard for TMV or DMV master mixing valves, which thermostatically blend hot and cold water to ensure safe delivery throughout hot water distribution systems, is ASSE International (ASSE) 1017-2009, Performance Requirements for Temperature Actuated Mixing Valves for Hot Water Distribution Systems. The standard has withstood the test of time and is widely accepted by mixing valve manufacturers as a requirement for market entry. The standard is inclusive and permits certification of TMV master mixing valves and, more recently, DMV master mixing valves.
ASSE 1017 is scheduled for an update and there is a growing constituency who believe that a new standard should be developed specifically for DMVs to keep pace with the technological advances within the water temperature control space. If a new standard is approved for development by ASSE, there are three components of the existing standard, at minimum, that should be considered for revision in a new standard tailored for DMVs.
First, TMV packaged assemblies with flow capacities > 40 gpm are currently permitted under the standard if they can control outlet water temperature within +/- 7°F of the set point. Given that DMV control is well within +/- 3°F of the set point, it makes sense to set a higher bar for this technology.
Second, TMVs typically have a minimum approach temperature of 15°F to 25°F. This is also referred to as a minimum inlet to outlet temperature differential. This means that for a TMV, the hottest mixed hot water temperature is about 20°F less than the incoming hot water temperature. For example, if the water heater is set for 140°F, utilizing a TMV with an approach temperature of 20°F, then the hottest possible outgoing mixed temperature is 120°F. For systems that want more flexibility in their outgoing water temperature, this could be a limiting factor.
Finally, under the current standard, a mixing valve primarily destined to be installed in a recirculating hot water system is laboratory tested in a three-way “dead leg” configuration, with an allowable differential between the cold inlet and mixed water outlet temperature of 30°F — a dynamic that is not a norm in a recirculation application, as it does not account for recirculated return water temperature. Most DMVs available can manage a system return temperature within 5°F of set point. That is not possible for a TMV, so a suggestion is that the current 30°F differential should be reduced to 5°F in the new “digital” standard.
Continuous Recirculation
There has been a change in thought regarding energy codes that mandate recirculation pump shutoff during periods where the hot water system is not in use. More and more industry professionals are raising concern that a switched-off recirculation pump offers minimal energy savings and may cause hot water system temperatures in some branches to creep into a range where waterborne pathogen amplification is possible.
There is a growing number of plumbing engineers who believe that hot water system recirculation pumps should operate continuously, must not be accessorized with an aquastat programmed to turn off at or above mixing valve set point temperature, and should be exempt from energy conservation measures, especially in facilities with immunocompromised populations. These individuals are also getting more vocal, proposing multiple code changes at the 2024 UPC® Code Hearings. At a fundamental level, continuous recirculation meets basic hygiene, comfort, and convenience requirements at the system user access points, such as taps and showers. Simply put, the expectations of the public is that one should not have to wait for hot water at a fixture; however, there is much more to it than that. There are energy and resource conservation issues if water must first run to drain for a period of time before hot water arrives. There are infection control concerns if hot water in the system is set to or can cool to Legionella incubation temperatures. And it is a generally accepted principle by those with expertise in waterborne pathogen control that continuously moving water mitigates biofilm (the pathogen food source) attachment within the pipework.
Third Party Support
OSHA: “Running domestic hot water recirculation pumps continuously to avoid stagnation” … “This may include excluding these pumps from energy conservation plans.”
ASHRAE Guideline 12-2020: “… recirculation helps reduce water age (stagnant water) relative to uncirculated systems” … “Turning off hot-water circulating pumps intended to save energy may result in temperatures favorable to Legionella growth.”
US Veterans Administration (VA): “Hot- and cold-water distribution systems shall be continuously recirculated.”
National Institutes of Health (NIH): “Continuous circulation is required to limit cooling and stagnation” … “Pumps serving systems operating at temperatures 60 °C (140 °F) and below shall provide continuous system recirculation, without aquastats or timers.”
Specific links to the locations of content on websites of the constituency above are located at the end of this article, but the messaging is clear — keep the pumps running.
From a plumbing engineering perspective, there is also a case for not shutting off the pumps — in designing hot water return systems, Hardy-Cross methodology should be followed. This means that through multiple iterations of fine-tuning the flow rate, velocity, pressure drop, and temperature drop, an “ideal” solution for the entire hot water return system (including each parallel branch) can be reached. If the temperature drop is engineered to such an accurate degree, then the hot water return pump, in practice and not just in theory, should never be turned off, as it is replacing very close to 100 percent of the heat loss. One problem is that there are a number of engineering practices that encourage the use of “rules of thumb” sizing for heat loss. These most likely lead to gross oversizing, but also in some instances to undersizing the pump. For those cases where the pump is undersized, energy conservations further perpetuate growth conditions. However, for grossly oversized pumps (e.g. 150 percent over flow capacity), an aquastat, at first glance, appears to make sense — it turns off the pump when temperature is met. However, especially as many hot water return systems are not properly balanced, “short-circuiting” of hot water temperature is likely, and some parallel hot water return branches are likely in danger of stagnating and promoting bacterial amplification.
Digital Technology Responds to a Paradigm Shift
With a growing concern of waterborne pathogens, and the introduction of ASHRAE 188, Legionellosis: Risk Management for Building Water Systems, and other water management plans, the plumbing landscape has changed. Fortunately, at the same time, the introduction of digital technology within plumbing has responded to this need. While user comfort and safety were first advanced in the early 2000s, the vision at this time is much more imaginative, using digital technology to optimize hot water systems. Digital technology in wider application, such as mobile communication, automotive, medical equipment, and now water temperature controls, is essentially “information management.” Collecting, interpreting, and managing data input with a high level of speed and accuracy that improves performance — in the plumbing industry, countless installations verify that DMVs do exactly that.
A move toward electronic actuation of existing TMVs commenced and has in many ways occurred as a result of the need to meet water management plan requirements, along with the desire to better track data. More and more new market entrants offering DMVs and stations give the impression that the central recirculation system space is progressing from thermostatic to digital.
Today’s advanced DMVs feature a hydraulic design that can operate with minimal inlet/outlet temperature differentials. With the addition of on-board thermistor-based temperature recognition componentry, and by deploying a series of algorithms to coordinate proportional blending, DMVs deliver an entirely new level of hot water system temperature control. A series of on-board programmable features and options allow the DMV to be customized to suit the hot water ecosystem within which it is installed.
Monitor, Record, and Document
The building automation systems (BAS) in larger institutional facilities is a busy information highway that carries a lot of responsibility for data collection and interpretation within the building utility infrastructure. In other words, it is a highly active network and the greater the responsibility it is given, the more the operator is at risk for information overload. Alerts once considered vital to the operation of the building utility systems can report in with such frequency and with such volume that they are subject to triage based upon available resource. This could compromise hot water guideline compliance.
A DMV has the capability to use the exact same information it is collecting to make the decisions required to keep water temperature at a programmed set point and use it to make the DMV an integral component of a hot water system risk management plan — a Standard of Care. Real time system monitoring, long term record keeping, and documenting performance are key elements of ASHRAE 188, which has become a foundational document of an active facility water safety management plan. An alternative is to send facility staff out to measure and document temperatures; however, this can be costly for a facility and results can be erratic — especially if a different “emergency” pulls the facility staff away from documentation duties.
Data storage is cloud based and can be maintained for as long as building management determines, which some legal experts would suggest extends to the seven-year statute of limitations prominent in personal injury law. Reports can be created on demand or with programmable frequency across a specific time period, as determined by facility operations management, to validate performance.
New software that seamlessly integrates with the DMV to provide dashboard monitoring exists, which can be both PC-based and smartphone/tablet enabled. Multiple hot water systems, buildings, and campuses can be viewed simultaneously or filtered based upon setting preferences. Alerts, whether they are DMV component self-diagnostics, service reminders, or a hot water system setting compromise, such as a hot water supply that has dropped below the 140°F prescribed by ASHRAE Guideline 12, can be received and managed in a variety of communications.
Clearly, the technological advances that produced digital water temperature control can be implemented in a broader spectrum of services well beyond the base plumbing device hardware. Information management, in the form of advanced software designed in concert with the DMV, can be deployed to support responsible hot water system management and enhance user safety.
DMV Limitations
The typical limitation for DMVs, in today’s climate, is cost. A DMV, with its advanced functions, typically costs more than a TMV. For building owners who are focused on construction budgets, even to the detriment of operating budgets, DMVs are often seen as an “extra” expense. However, even here, due to litigation concerns arising from legionella or other waterborne pathogen outbreaks, there is opportunity. DMVs are very easy to retrofit into existing infrastructure, whether or not it includes an existing TMV. And often, operational budgets allow for higher priced options if deemed necessary.
Another limitation of DMVs is that they cannot control the temperature in every individual branch of the hot water return system. Good engineering, construction, and commissioning practices are required for hot water return systems regardless of the use of a DMV or TMV (or in some cases neither).

ASSE 1070
No discussion of water temperature control and system design is complete without some commentary on point of use control. ASSE 1070-2015/ASME A112.1070-2015/CSA B125.70:15, Performance Requirements for Water Temperature Limiting Devices, a standard that is referenced in the Uniform Plumbing Code® (UPC), is excerpted as follows: “Hot water delivered from public-use lavatories shall be limited to 120 °F (49 °C). The maximum temperature shall be regulated by one of the following means. (1) A limiting device conforming to either ASSE 1070/ASME A112, 1070/CSA B125 or (2) A water heater conforming to ASSE 1084.”
The definition of “public use,” per the UPC, is “Applies to plumbing fixtures that are not defined as private.” “Private use” is explained as “Applies to plumbing fixtures in residences and apartments, to private bathrooms in hotels, hospital, and healthcare facilities and to restrooms in commercial establishments where fixtures are intended for the use of a family or an individual.” A concept is that to reduce water temperature at a lavatory to either a required code or to a building management preferred temperature requires a small under sink TMV. A TMV at a point of use has two primary functions. First, to adjust the proportion of incoming hot and cold water to maintain a fixed outlet temperature. And second, to shut off an incoming supply in the event of a failure of the opposing supply.
Like with any technology, there are always trade-offs to be considered and point of use TMVs are no exception. These have been identified by Dr. John Lee, a leading global expert, as a potential Legionella incubator. That is because in recirculating water systems they maintain warm water stagnancy points between the TMV and the recirculating hot water supply, and the TMV and the fixture. In fact, according to Lee, the actual TMV itself presents a warm, comfortable bacterial incubation environment.
In addition, point of use TMVs in recirculation systems may exacerbate the system maintenance requirement (e.g. some facility owners claiming they need to be replaced every one to three years) and, without a manual override, will prevent thermal disinfection of the pipework leading to them, to the fixture, and the fixture itself.
Where point of use protection from higher temperature recirculating hot water is required, a new ASSE 1070 compliant point of use technology that is effectively a DMV “micro-sized” and fitted into a faucet is now available. The fixture can be networked to provide all of the control features, benefits, and positive user outcomes of the time-proven DMV, and adds a programmable periodic “duty flush” to move stagnant dead legs to drain and a completely hands-free flow activation and temperature adjustment.

Bringing Together Advanced Technology and System Design
With self-contained compact DMVs available in a variety of sizes, more in the new product development pipeline, and new performance-matched point of use digital faucet technology, the plumbing system designer can now deliver a high-performance hot water system optimized to the building form, function, and size to make every hot water system design digital. After years of stagnancy (pun intended), plumbing systems are rapidly entering the 21st century, in large part to respond to water quality concerns.
System designs that enable the building operator to comply with a Standard of Care are viewed as a positive outcome by Legionella management consultants. Whether operators are charged with managing utilities in a 1,000-room casino hotel, a 20-story hospital, a K-12 school, a college campus with 100 buildings, and everything in between, digital water temperature control with matching software operating in concert with, independent from, or placed in buildings that do not deploy building automation, is one of the most significant advancements the plumbing industry has experienced this century. What an incredibly exciting time to be part of our industry!
But with those changes, codes and standards need to shift with the new environment. And in some instances, new standards are needed to properly address new technologies. In this case, some extra thought should be encouraged in developing a new standard for this new technology — especially as these new technologies can be an integral part of a solution to a Legionella issue that is not going away anytime soon.
References
OSHA: https://www.osha.gov/legionnaires-disease/control-prevention#hotwater ASHRAE Guideline 12-2020: https://www.techstreet.com/standards/guideline-12-2020-managing-the-risk-of-legionellosis-associated-with-building-water-systems?product_id=2111422 ASHRAE 188–2018: https://www.techstreet.com/ashrae/standards/ashrae-188-2018?product_id=2020895 CDC: https://www.cdc.gov/legionella/resources/guidelines.html Veterans Administration: https://www.va.gov/vhapublications/ViewPublication.asp?pub_ID=9181 Joint Commission: https://www.jointcommission.org/standards/prepublication-standards/new-water-management-requirements National Institutes of Health: https://www.orf.od.nih.gov/TechnicalResources/Pages/DesignRequirementsManual2016.aspx Article by Paul L. Knight first appeared in Working Pressure magazine
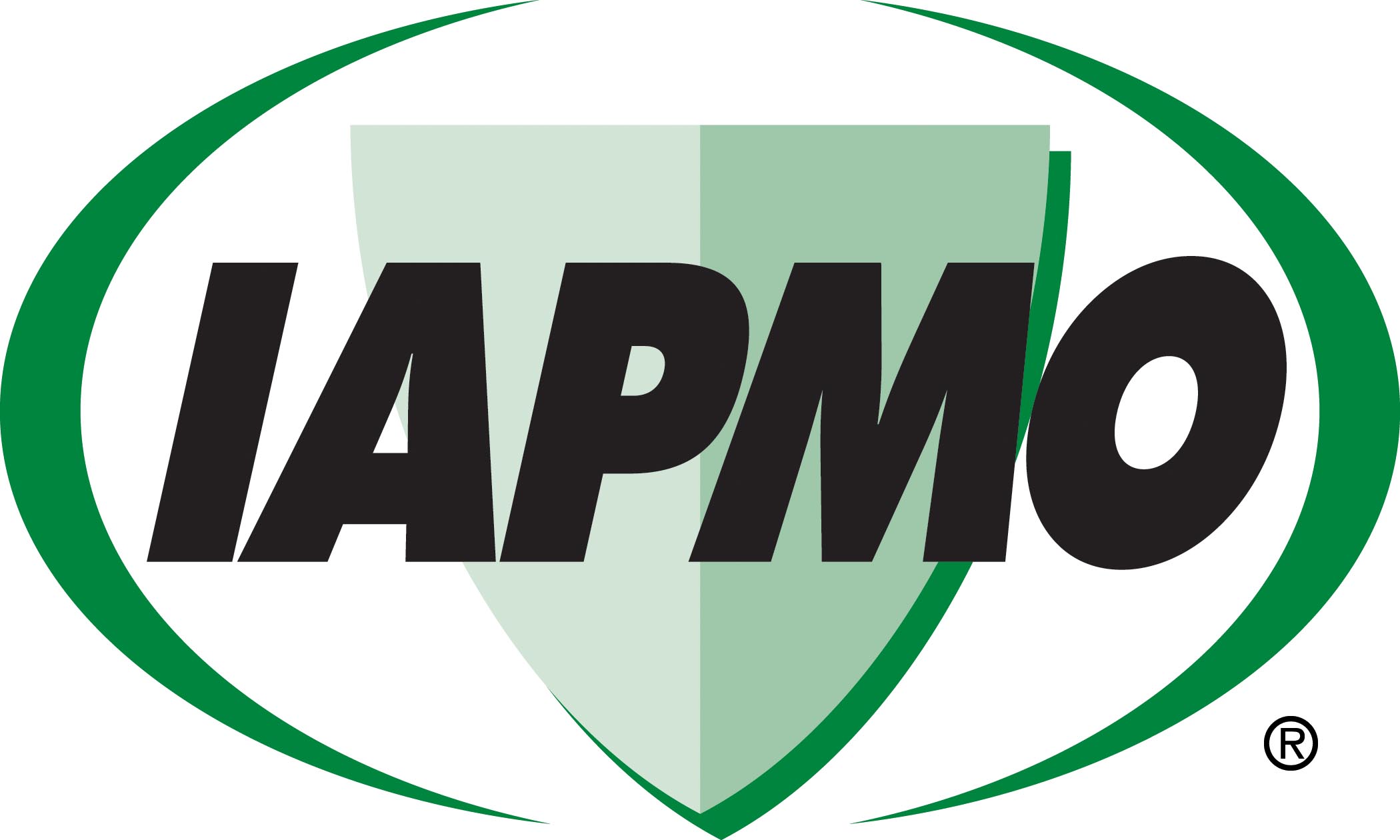
IAPMO
IAPMO develops and publishes the Uniform Plumbing Code®,the most widely recognized code of practice used by the plumbing industry worldwide; Uniform Mechanical Code®; Uniform Swimming Pool, Spa and Hot Tub Code®; and Uniform Solar Energy, Hydronics and Geothermal Code™ — the only plumbing, mechanical, solar energy and swimming pool codes designated by ANSI as American National Standards — and the Water Efficiency Standard (WE-Stand)™. IAPMO works with government, contractors, labor force, and manufacturers to produce product standards, technical manuals, personnel certification/educational programs and additional resources in order to meet the ever-evolving demands of the industry in protecting public health and safety.
Last modified: December 30, 2022