With things moving toward a new normal and the COVID situation becoming more under control in many areas, we are again on the road conducting training and certification across the nation. Looking back at the changes that have taken place since March of 2020 drives home the need to continually adapt to the challenges that occur in our ever-changing world. We need to always be proactive in everything we do — anticipate problems before they happen and have solutions ready to mitigate or prevent the damage that may take place as a result of any issue that occurs.
That idea is what the American Society of Sanitary Engineering, now known as ASSE International, was founded on back in 1906. The ASSE motto, “Prevention Rather Then Cure,” is what backflow prevention and cross-connection control are all about. We use backflow prevention methods, devices, or assemblies to ensure that our water systems are protected from any threat. To do that, we need to look at many variables and possibilities — look at actual and potential hazards. We need to expect the unexpected and make provisions to deal with any hydraulic situation that occurs. In this field, you need to think creatively and look at every situation as unique.
Over the years, I have been fortunate to collaborate with so many talented craftsmen. My career in the construction field allowed me to work on a variety of jobsites, both large and small. From single family homes to nuclear power plants, it has been an interesting ride. Being an apprentice and journeyman instructor with the plumbers and pipefitters union allowed me to also play a role in influencing the career paths for many individuals. Many of the individuals I worked with or trained were true artists when it came to installing systems. No offset too difficult to make, they could take a shop drawing or a blueprint and create a piping system installed to the exact specification that appeared in the documents they were provided. They built an exact replica of the drawing itself and did it with quality and precision that was second to none.
As installers, they were everything you’d hope they would be. But what if the drawings were incorrect? What if there was a mistake in the engineering? What happens when, as we sometimes say, the wheels come off the bus? Did they have the natural curiosity to go beyond the installation and insist on understanding the systems themselves? That is when we need to look beyond drawings and specifications and understand the systems and components themselves. This is when the true craftsman emerges. This is where we find the people who make our industry work.
In the backflow prevention world, installers, repairers, testers, and surveyors need to look beyond shop drawings and plans. We need to develop an understanding of the systems we are tasked to work on. We need to look at each piece of the puzzle, even when we are simply preforming an annual test on a previously installed assembly. Evaluating a backflow prevention assembly is so much more than simply opening test cocks and following a field test procedure’s exact steps. A quality tester understands that the actual testing procedure is not the first step in conducting the evaluation of the backflow prevention assembly — in reality, it is one of the last steps. It is also not the most critical part of the evaluation. Before we even open our test kit, we need to answer a number of questions.
Is the assembly selection correct? To answer that, we need to know the degree of hazard of the system the assembly is installed on. Is it high or low? Is it a danger to the health of people, or will a backflow occurrence simply effect the smell or taste of the water supply? We can’t assume that the installer was correct in his valve selection decision unless we understand the hazard presented. Once we understand the degree of hazard, we can move on to the next questions.
What are the possible hydraulic conditions? Is this a direct or indirect connection? Do I need to be concerned about backpressure or backsiphonage? Or are both possible? Remember that proper cross-connection control requires us to install the proper protection for each individual service or connection. We do not function in a one-size-fits-all world. If the connection can be properly protected with a hose-bibb vacuum breaker, then a reduced pressure principle assembly should not be installed. While we should always error on the side of caution in selecting the proper protection, we should not simply use the highest level of protection everywhere, as that can also lead to other unnecessary problems and concerns.
“Prevention Rather Than Cure”
ASSE 1011 Hose Connection Vacuum Breaker
ASSE 1013 Reduced Pressure Principle Backflow Prevention Assembly
Water Hammer
“Prevention Rather Than Cure”
ASSE 1011 Hose Connection Vacuum Breaker
ASSE 1011 Hose Connection Vacuum Breaker
Once we know that the correct assembly type was installed based on our understanding of the degree of hazard and the type of backflow the system may be subjected to, the next questions are: Has the assembly been installed correctly? Is it installed in the proper orientation? At the correct height with the correct clearances? Does the location have the proper drainage capacity? While backflow testers do not have the power to order building owners to comply with code regulations or installation standards, the tester has a duty and an obligation to report deficiencies to both the building owner and the Authority Having Jurisdiction. Pointing out that a reduced pressure principle assembly does not have the proper drainage can protect a building from damage or flooding, and will also protect a tester from liability if the valve fails and damage occurs in the future.
The tester must also understand the hazards that may be present while assessing the assembly. Are there electrical hazards? Are there confined space issues at the location? Are lifts or ladders required to perform the testing? Vehicle traffic, insects, noise, and any number of other safety issues that the tester must consider before the testing begins may be present. Once these factors are all considered and dealt with, the field test can begin.
Once the field test is complete, a skilled tester does more than simply record the results. The tester must understand what the reading itself means and, in the case of a component failure, why that failure occurred. Recording on your test report that a check valve leaked or failed is only the beginning of your thought process. Why did it fail? What can be done to prevent a failure in the future? If the second check of a double check valve assembly or a reduced pressure principle assembly fails when it is field tested, we need to understand why. If the check is disassembled and we find dirt or debris in the check, then flushing the assembly and cleaning or replacing the disc may solve the problem. What if the check valve is broken, or the disc has been ejected from the disc holder? Replacing the check assembly will allow you to retest the assembly and get a passing value on the check valve. But did you solve the problem? The answer is no. You simply treated the symptom; you did not cure the disease. A quality tester or craftsman would work to discover the hydraulic condition that caused the failure and correct it to prevent future failures. Identifying the problem and then making recommendations to the owner on how to ensure the problem does not happen again is what should happen.
The technicians who do this are the ones we want. That is how we should train and mentor individuals to be. Teach them to understand the system, not just the assembly. We should always be asking the question of why things happen. Do not simply look at the current situation — look at the causes and the effects, and look for solutions to problems that have occurred, or may occur in the future. Be proactive in everything you do and always remember the ASSE Motto, “Prevention Rather Than Cure.” It is what cross-connection control and backflow prevention are all about.
Article first published in Working Pressure magazine
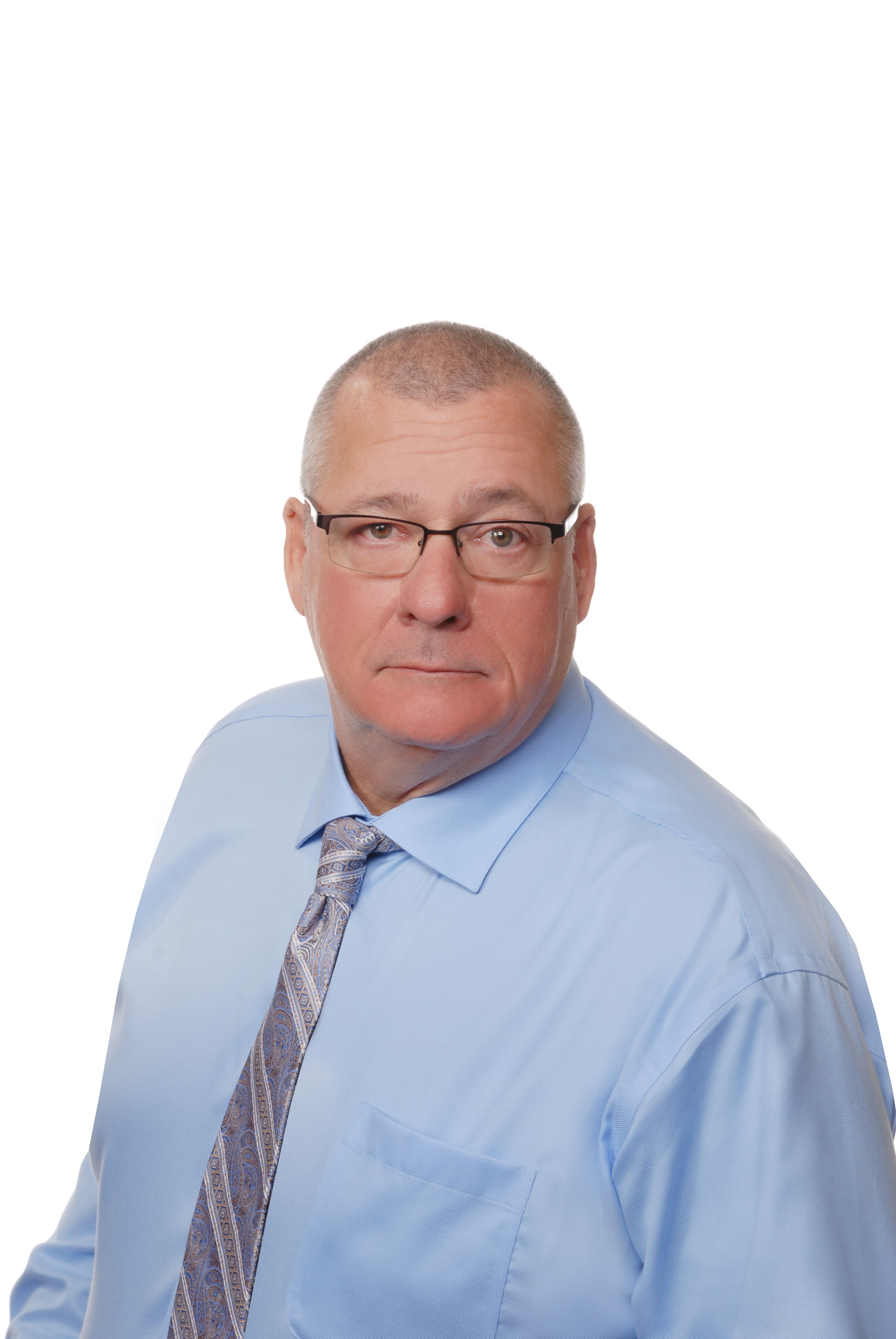
Sean Cleary
Sean Cleary has been a member of United Association Local 524 Scranton, Pa. for more than 40 years. He has worked in all phases of the plumbing and mechanical industry, and is a licensed master plumber. Cleary is a past president of ASSE International and past chairman of the ASSE Cross-Connection Control Technical Committee. He is employed by IAPMO as the vice president of operations for the Backflow Prevention Institute (BPI).
Last modified: December 19, 2023