In North America, the economies of the United States and Canada are very closely tied. The products in both marketplaces are frequently either very similar or often the same. This is especially true for plumbing products. The accessible materials and technologies combined with the application of the product(s) dictates end-design. There is nothing with regard to country unique about the systems in which these products are installed.
At the turn of the last century, the installation of plumbing in homes and buildings became more prevalent. The complexity of these systems and products increased. It was also at this time that the concerns with cross contamination and safety of the installed systems were being voiced. It was clear there was a need for expanding the plumbing codes, which lead to the development of product standards to supplement the codes.
The need to develop performance and safety standards to further enhance the existing plumbing codes was realized in both the United States and Canada. The need for standardization to ensure all components were compatible with each other and that they operate to a minimum level of performance were central aspects of these standards.
Both countries set about to independently develop product standards. The result is that there existed two different standards for the same products, as required by each country, respectively. The physics and engineering principles that drive the design of plumbing components was also important in defining critical aspects of each product’s performance. The result was that basic parameters and functions requiring evaluation were essentially the same.
However, the methods to demonstrate compliance, the parameters measured and the criteria between the two national standards, varied. Oftentimes the differences were subtle. Example: To perform a life cycle test evaluation of a supply fitting; in the United States, the test was run at 50 psi static pressure, while in Canada it was run at a flowing pressure of 50 psi. While this may seem minor, it is a difference. In other instances, the differences are more substantial and not as easily reconciled.
This is not to say that one set of standards is better than the other. They are equal; they each used a sightly different approach to achieve the same end goal — standardize compatibility of products to achieve a minimum acceptable performance.
WHY IS THIS IMPORTANT?
Many manufacturers, who made and sold the same products in both countries, would be required to have products tested and evaluated in each country by two different certifying and testing agencies. Often, this resulted in maintaining two separate inventories for the same products. During the design process, engineers need to be aware of and design to slightly different requirements. This only complicated the logistics of getting products to market and added cost due to duplicating the product approval process across both countries.
Many manufacturers, who made and sold the same products in both countries, would be required to have products tested and evaluated in each country by two different certifying and testing agencies. Often, this resulted in maintaining two separate inventories for the same products. During the design process, engineers need to be aware of and design to slightly different requirements. This only complicated the logistics of getting products to market and added cost due to duplicating the product approval process across both countries.
Starting in the last part of the 20th century, trade agreements between the United States and Canada began to open the markets for plumbing products. The first benefit resulting from these agreements was that the manufacturers did not need to use two distinct agencies to certify their product. Agencies in each country could certify for the other country. With this convenience, it soon became apparent that the products still needed to be tested twice, since there were still two mutually exclusive standards.
It was during this time when the full benefit of harmonization was realized. The goal was to harmonize the standards so that there was one standard that served both countries. This would streamline the process, require only one set of tests for certification for both countries. And this could be achieved by using only one certification body.
There are several other subtle advantages that were of benefit to other sectors of the market. The beneficiaries include the standards development organizations (SDOs), plumbing officials, and consumers. The obvious benefit to manufacturers is the fact there is less testing required for certification. There is no need to inventory product based on country. This also opens the opportunity for the full portfolio of products to be available in both marketplaces. Wherein the past, some models would only be available in one market due to constraints with dual certifications. During the product development, design engineers only have one set of design criteria, removing some complication common to R&D. All of this results in lower cost of manufacturing, which will favor the consumer in product variety and prices.
Having a single standard for both countries allows for the listing of product to be to this single standard. This aids plumbing officials in removing the complication of multiple listing to different sets of requirements. The certification marks can show compliance for both countries.
Additionally, the SDOs can draw from a larger pool of expertise (volunteers from both countries) to assist in the development of standards. The process also utilizes the best practices of each SDO for development. These two factors contribute to a timelier release of revisions and improved standards.
The harmonization of ASME A112.18, Plumbing Fixture Fittings, and CSA B125, Plumbing Fittings, was the first pair to undergo the process. The goal was to harmonize the standards by symmetrizing the two standards into one that served both countries. The result was ASME A112.18.1/ CSA B125.1, Plumbing Supply Fittings.
This first attempt at harmonization was a very large undertaking. Nearly 100 volunteers worked for nearly seven years to publish this standard. Other ASME/CSA standards soon followed. With each iteration, the learning from the previous activities facilitated improvement in the working procedures. Today, the harmonization of two standards can be accomplished in two years or less.
While ASME and CSA were the pioneers in harmonizing plumbing standards, other SDOs, including IAPMO and ASSE, have joined the efforts to harmonize their standards. These harmonization activities are no longer limited to harmonization across national boundaries — harmonization between domestic SDOs is now common. This is important in eliminating the duplication of similar standards and providing clear understanding on what requirements a product must meet.
ASSE International, as mentioned above, has also been engaged in many harmonization activities. ASSE currently has four published harmonized standards. These are considered tri-harmonized standards, as they are the work of three SDOs coming together to develop a single standard. These harmonized standards are partnerships between ASSE, ASME and the CSA Group and include ASSE 1002/ASME A112.1002/CSA B125.12, Anti-Siphon Fill Valves; ASSE 1016/ASME A112.1016/CSA B125.16, Automatic Compensating Valves for Individual Shower & Tub/Shower Combinations; ASSE 1037/ASME A112.1037/CSA B125.37, Pressurized Flushing Devices for Plumbing Fixtures; and ASSE 1070/ASME A112.1070/CSA B125.70, Water Temperature Limiting Devices.
Recently, ASSE has entered into an agreement with the CSA Group to harmonize three additional standards that are overlapping. ASSE 1003/CSA B356, Pressure Reducing Devices, has been under development and is expected to publish mid-2023. Also in the works is ASSE 1013/CSA B64.4. This standard covers the performance requirements for Reduced Pressure Principle Backflow Prevention Assemblies. Once this standard nears completion, work will begin on ASSE 1015/CSA B64.5, Double Check Backflow Prevention Assemblies.
At this time, there are not any other standards in queue to be harmonized. However, there are many other standards that would be good candidates. As the work underway is completed and the benefits from this activity realized, the harmonization of standards will continue to be explored.
This article first appeared in Working Pressure magazine.
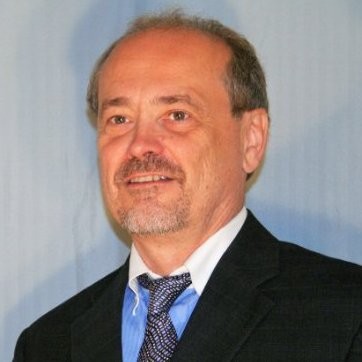
Terry Burger
TERRY BURGER, ASSE International Director of Product Standards, has been working in the plumbing industry since 1994. During that time, he has worked in the areas of product development, quality, testing, and compliance. Burger earned an engineering degree from Case Western Reserve University and an MBA from Cleveland State University. Prior to working in the plumbing industry, he worked in the nuclear power industry for nine years as a chemist and was enlisted for six years in the U.S. Navy in the submarine service.
Last modified: December 19, 2023